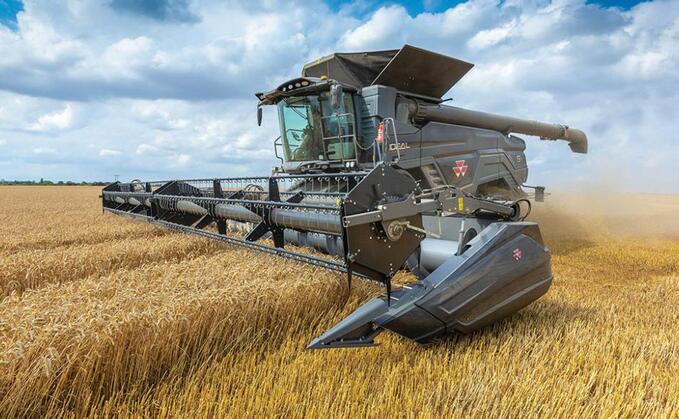
As harvest draws to a close around the country, Agco was showing of its new Ideal combines in a thick crop of winter wheat in Lincolnshire.
Alex Heath went to see the new contender...
Aiming directly at the high capacity combine harvester sector, nothing about the Agco Ideal is small, including the £200 million investment in bringing the graphite coloured monster to market.
In 2011, Agco tasked its factories around the world with the job of building the machine from the ground up.
Fendt's Marktoberdorf factory was responsible for the cab and electronics; Massey Fergusson's Hesston factory, the grain handling system; and Challenger's Jackson facility oversaw the new track units.
By using all its facilities, Agco says it has manufactured a combine which performs efficiently and reliably anywhere in the world. Time will tell on that, however the engineering which has gone into producing the output figures they are now quoting is certainly impressive.
Agco says by 2022, 67 per cent of the combine market will be in classes seven, eight and nine, so its efforts have focused solely on this area. While not everyone will be familiar with the combine class categories, it essentially relates to engine power.
Ideal combines are handily labelled with the class number, aiding simplicity of decision-making. And although the flagship Ideal 9 sits in class nine, Agco claims it could go toe to toe with any class 10 machine and prevail.
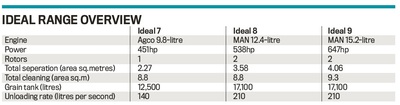
ROTORS
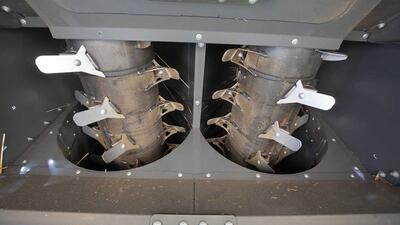
Taking care of the threshing and separation, Agco has designed the longest rotors on the market at 4.8 metres. The rotors are 600mm in diameter, which Agco says provides a good mix of centrifugal force and concave separation.
Dubbed Helix, the Ideal 7 has a single rotor, while the 8 and 9 have dual rotors. Leading the way is the feeding rotor. This runs at 70 per cent of the threshing rotors' speed and is proportionately controlled, so if the rotors slow down, the feeding rotor slows too.
Threshing is courtesy of two banks of four rasp bars per rotor and is responsible for 70-80 per cent of grain separation. The threshing zone measures 1,228mm long, which equates to 1.66sq.m of threshing area on the two biggest models and 0.83sq.m on the smallest.
Each rotor has four individually adjustable concave sections which are easily removed for maintenance and provide a maximum concave gap of 35mm.
The separation section extends to 2,460mm in length and offers 1.44sq.m on the 7, 1.92sq.m on the Ideal 8 and 2.4sq.m on the 9. The rotor fingers measure 140mm and are angled towards the rear of the machine at a patented 20 degrees.
Energy efficient
Agco says this gently divides the crop between the helix sections of the rotor, reducing the chances of the crop sticking to edges and blocking the machine.
The arrangement is said to be energy efficient, with rotor speed of 400-920rpm on the 7 and 280-1,160 rpm on the dual rotor models.
CLEANING
Catching the grain is a pair of plastic pans. The front pan feeds the grain into the front and centre of the cleaning system while the rear one feeds the outer sections. This configuration is said to evenly distribute the grain on to the sieves, even on slopes of up to 15 degrees.
This is a standard feature on the Ideal 8 and 9 and a variation of this can be specified for the single rotor model. Using plastic in the pans has made them much lighter, 22kg for the front and just over 50kg for the rear one, enabling one person to remove them.
Rattles and vibrations are practically non-existent as a result and rusting is a thing of the past.
Spreader
The Ideal offers the longest sieves on the market, with the Ideal 7 and 8 sharing a 2.01-metre set while the 9 goes to 2.21 metres.
Total sieve area on the Ideal 9 is second only to New Holland's biggest machines at 5.40sq.m while the total cleaning area measures in at 9.30sq.m. On the 7 and 8 the sieve area is 4.90sq.m and the total cleaning area is 8.80sq.m.
The 150mm sides between each trough are designed to eliminate any interference while going across slopes.
Three fan units capable of 250-1,400rpm blast air at the chaff and straw, separating most crop by the first drop in the sieve set-up. Long fingers protruding off the back of the preparation floor hold up short straw, which is then removed by the high pressure air.
Most of the chaff is spread through openings above the rear wheels, with the rest passing through to the chaff spreader at the back, which can be configured to put chaff through the chopper, into the swath or spread.
There are two options when it comes to choppers. The standard BaseCut features 56 knives in four rows, while the ShortCut option has 112 across eight rows. Both units will run at either 850rpm for crops such as beans or maize, or 3,600rpm for cereals and oilseed rape.
This is changed by moving the drive belt. The chopper can be put in or out of work from the cab and has the capacity to spread a lot further than 12.2 metres (40 feet) says Agco.
Individual disc speed adjustment allows to compensate for wind direction and a nifty inclusion is automatic switchover when a headland turn is made, ensuring the material is always thrown in the right direction.
GRAIN TANK AND UNLOADING
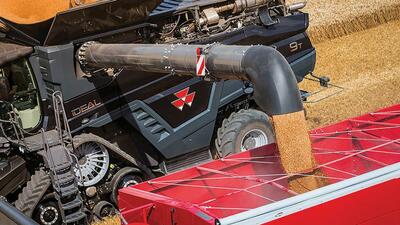
One of the biggest talking points surrounding the Ideal is its gargantuan grain tank, named the Streamer 210.
Capable of packing in 17,100 litres, or about 12 tonnes, it is some 2,600 litres bigger than its nearest competitor. To transfer such a quantity of grain, Agco has developed a 210 litre per second auger, which can unload a full tank in about 82 seconds.
The key to the voracious appetite of the auger is its 480mm diameter and relatively few flights, enabling a low rotation speed and consequently low power requirement. Agco says 3-4hp per 100 litres is used powering the biggest auger, equating to a maximum of 8.4hp to operate.
Power requirement
The smaller tank and auger, named the Streamer 140, can hold 12,500 litres and unload at 140 litres per second. Auger lengths available are 7.6, 9.15 and 10.6 metres.
In the bottom of the grain tank are two augers which feed the lifting auger. Grain gates in the bottom of the tank ensure the cross augers are not overwhelmed with grain and can be adjusted to limit the flow of grain, when topping trailers up for example.
The turret-style auger can also be only partly folded out, to allow for trailers to pull in between the combine and header, useful for opening out and on headlands. As the augers are so long, the rear portion folds behind the combine.
To not get on the wrong side of any patents, the Ideal's auger folds to 75 degrees.
ON-BOARD TECH AND USABILITY
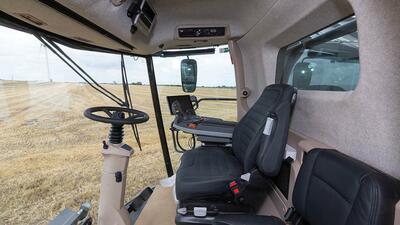
In the depths of the Ideal are 52 mass acoustic detection sensors (MADS), providing a real-time visualisation of what is happening in each section of the rotors, pans and sieves. The sensors can pick up what is landing where and adjustments are automatically made.
For instance, the sensors can differentiate between clean grains, broken grains, straw and unthreshed heads, so sections of the threshing, separation and sieve system can be reconfigured automatically. Agco calls this IdealHarvest.
It shows where in the system grains are being separated by producing a curve which, the manufacturer says, will reduce losses before there is any sign of crop going over the back.
It runs separately form the main terminal on a tablet using the company's SmartConnect app and is linked to the machine's onboard Wi-Fi.
Control
This means the control of the combine's grain systems can be controlled remotely by the farm manager if an inexperienced driver is operating, or a master/slave system could be used if running more than one combine.
Also feeding data into the software is a grain quality camera which determines how clean the sample is.
The operator can then select objectives, be it throughput, straw quality, sample cleanliness or fuel efficiency.
The cab is based on that of a Fendt Rogator, with the armrest and console being borrowed from Fendt's Katana forage harvester. Operator comfort is a top priority and it really shows, with vast expanses of glass, extending to 5.75sq.m and a noise level of just 73dB.
Other nice features for the operator include a leather seat, a cavernous fridge and 360-degree camera to keep the bodywork safe.
ENGINE
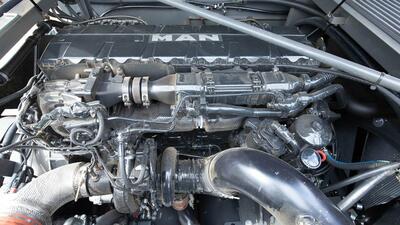
Each model uses a different power plant, the Ideal 7 using Agco's own 9.8-litre block pumping out 451hp; the 8 using a 12.4 MAN block realising 538hp and the flagship 9 again using a MAN, this time a 15.2-litre unit topping out at 647hp. All engines meet Stage 4 emission regulations.
AdBlue storage is 180 litres while diesel tank capacity is either 1,000 or 1,250 litres on the Ideal 7 and up to 1,500 litres on the 8 and 9 models.
Although no official figures have been released on fuel consumption, field testing and demonstrations have shown 75 litres per hour about the average according to Agco for diesel, while AdBlue is sipped at 2.5 litres per hour.
Ease of maintenance and reducing daily tasks was a major design task according to the manufacturer.
This can be seen in the engine bay where the cooling pack is located. The new AirSense cooling system features a 2.7sq.m radiator which is serviced by a 950mm diameter fan.
At various intervals the fan reverses, sending a massive plume of dust billowing into the air as the top grate is cleared. Agco says this system is so effective that blowing the radiator out is a thing of the past.
The engine is also kept near spotless from the air generated from this system. And the air filter only needs cleaning when an alert goes off in the cab, reducing daily servicing.
Greasing
Shortest interval for greasing on the combine is 50 hours, meaning the grease gun only needs wielding once or twice a week.
There are just 13 spring tensioned belts on the machine and a handy tension guide can be sighted from the ground, as can oil levels on all the gear boxes.
TRACKS
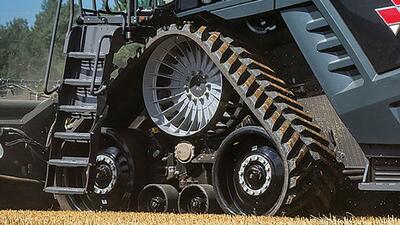
The main design point was to keep the machines designated with a ‘T', road legal on UK and European roads. This has been achieved, with the 660mm-wide track sitting at 3.3 metres and the 760mm at 3.5 metres.
There is also an option to go to 910mm, which sits on the road at 3.8 metres.
The sheer weight of the Ideal when full has meant focus has also been given to the footprint of the machine. For the narrowest track width, a total of 2.55sq.m of track is in contact with the ground, while 3.52sq.m is touching with the widest track.
The rear axle has not been neglected either with the option to equip it with 750mm-wide tyres. If tyres on the front are your thing, then up to 900/60 R38 boots can be fitted, again remaining under 3.8 metres transport width.
Tyres
Tracks feature closed circuit hydraulic suspension. The front idler roller is independent of the rest of the track unit, allowing it to climb up and over obstacles by opening out from the rest of the idlers. The two mid-idlers are attached to the arm of the rear idler and freely oscillate over contours.
Agco says this gives unrivalled operator comfort. Tension is provided by an accumulator and actuator plumbed into the suspension system. In keeping with the low maintenance theme, there are no grease points on the tracks.
How much will it cost?
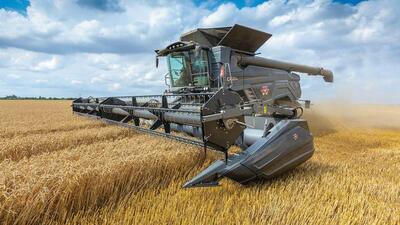
For the largest Ideal 9 machine on 660mm tracks (circa £60,000), with Streamer 210, SmartConnect, chop to drop residue system, 9.15 metre folding auger and Trimble GPS, you are looking at £499,680.
The 12.2m Power Flow header also costs £61,000.
Verdict
Agco expects to have between a dozen and 20 machines sold and working in the UK next harvest. The combine is certainly an impressive machine and what we have seen of its performance matches its on-paper credentials.
We understand many farmers who have seen the combine in action have also been impressed.
However, uncertainty over residual value and reliability seem to be the major challenges Agco needs to address to reassure customers the cost of ownership will be competitive.