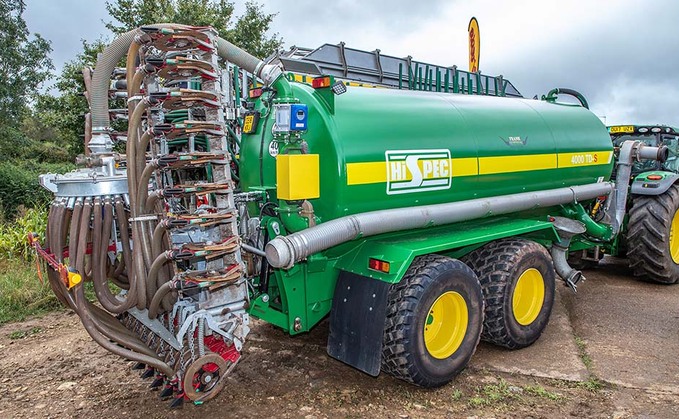
Applying slurry has become a lot more scientific for one Herefordshire grower, following investment in application equipment with NIR sensing. Geoff Ashcroft reports.
With the introduction of near-infrared sensing (NIR) for slurry applications, Herefordshire grower FM Green at Ditton Farm, St Owen's Cross, can now fully utilise the slurries it applies to stubbles.
"We do produce a lot of liquid from our 500kw on-farm AD plant," explains foreman David Tinton. "But we have only recently started to make the most of it, thanks to advances in NIR sensing on slurry equipment to determine exactly how many kilos of N are being applied."
Cropping extends to winter cereals, potatoes and oilseed rape, with maize and sugar beet grown for the AD plant. An on-farm chicken enterprise creates a plentiful supply of manure for inclusion with the digester.
While the majority of the potato crop goes for processing, farm owner Mark Green uses three varieties for his Two ÍæÅ¼½ã½ã crisps brand, which are cooked and packed on-farm. Surplus stock-feed potatoes are used in the digester, along with maize, sugar beet and chicken manure.
Mr Tinton explains; "In return, we provide power to the grid and get a supply of liquid digestate and organic matter that goes back onto our sandy soils.
"It is a volume that adds up to about 6,000 cubic metres of slurry, which is utilised in the same way as bought-in fertilisers.
"We have reduced our reliance on bought-in fertilisers, which are applied on a variable rate basis," he says. "Longer term, we would like to apply slurry using variable rates too."
Application is by an 18,000 litre (4,000 gallon) Hi-Spec vacuum tanker in combination with a Vredo 6m shallow disc injector, supplied by local dealer Frank Sutton. The outfit includes an NIR sensor on the outlet of the vacuum tanker in combination with a Krohne flow meter - both supply data via IsoBus that is used by John Deere's manure sensing software to determine the levels of N, P, K, ammonia and dry matter of the slurry, as it being applied.
"We have seen how variable the nutrient content of slurry can be," says Mr Tinton. "But with analysis at the point closest to application, this technology is able to react to continual changes in nutrient values as the liquid leaves the tank."
The NIR sensor takes 14,000 readings per second, to determine slurry content as it leaves the tanker. Using IsoBus control and a target application rate entered into the tractor's universal terminal, the NIR sensor will automatically control the tractor's forward speed through its continuously variable transmission to maintain the target application rate in response to fluctuating nutrient values.
Operator Jamie Gwillim says; "Live analysis of liquid slurry and automatic control of forward speed during application is simply incredible. My forward speed can automatically vary from 8-15km/h depending on what the NIR sensor sees."
The twin-axle tanker and 6m injector is pulled using a John Deere 6250R, which Mr Gwillim describes as comfortably on top of the job. "For all but the steepest banks, it is a combination that is maneuverable and offers low ground pressure thanks to the tanker's 710/50 R26.5 tyres and a following rear axle," he says. "The next 6250R will come with a ball and spoon coupling, to reduce movement through the hitch from the weight of the injector, behind the tanker. And the next tanker would be better with a hydraulically-driven pump."
When it comes to application rates, Mr Gwillim says the farm's agronomist provides a recommendation, with the value then entered into the tractor's control box. Typically, the liquid offers an average value of 3.4kg of nitrogen per cubic metre, with a nominal value for P and K.
"A target rate of 60kg of N per hectare equates to 17.6 cubes/ha, but the variability of nutrient can see the total liquid volume fluctuate to compensate," he says. "When the volume increases, the tractor's forward speed slows, and when the volume decreases the tractor will speed up."
Mr Gwillim says that the lower value of N in the liquid being applied compared to bagged fertilisers does see an increase in volume going onto stubbles. He says that there are occasions when the tractor cannot travel fast enough to apply the required volume of liquid.
"In these instances, I will reduce the gate valve and slow the flow rate," he says. "It just means I have to go back over those areas and re-apply to achieve the required rate."
He also limits the total volume applied to 35 cubic metres/hectare, to prevent over-filling the injector slot and avoid run-off.
"A wider injector would be the answer, but weight and physical size become more of an obstacle," he says.
"We do see the finished result in an application map, which shows where the volumes change to maintain the required value of N," he says. "As we progress to JDLink, the information should be easier to manage between tractor and farm office."
By injecting slurry, the farm says odour is also minimised, with the liquid digestate often incorporated by cultivator within 24 hours.
"Slurry is right there in the top 50-75mm for soil, ready for plant uptake," says Mr Gwillim. "We direct-drilled our oilseed rape this year and the crop got off to a flying start. It also adds moisture to a dry seedbed, and has been enough this year to get plants up and away from flea beetle attacks."
The farm has also invested in more storage capacity, strategically placed around the farm, to simplify logistics when it comes to applying liquid digestate. "We utilise the tanker through the winter to pull liquid away from the digester and store it in our lagoons," he says. "This lets us handle applications when we need them and not when the AD plant dictates."
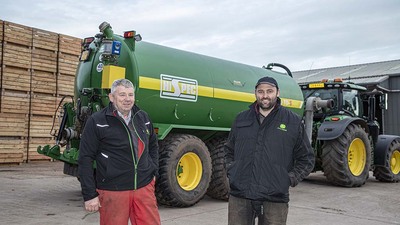
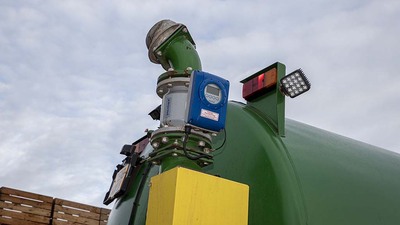
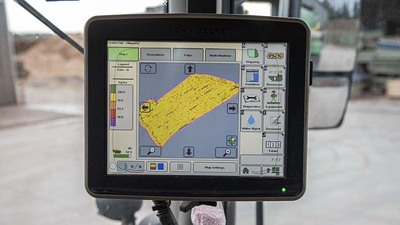
Verdict
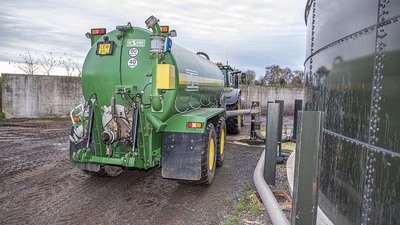
Prior to the arrival of the tanker and injector combination, application was by local contractor, using umbilical equipment.
Mr Tinton says; "There was always a risk of run-off with our rolling fields. Nutrient analysis was never very accurate, and we could sometimes see over-applying on headlands, which did lead to yield penalties in following crops."
Mr Tinton says a fast-fill pump and a quick-fill coupling sees the tanker filled in under two minutes. "It is a great system that has improved logistics and provided us with a known value on all our liquid digestate," he says. "We have also started to use it to supplement DAP for maize and sugar beet crops.
"Overall, we are applying accurately, efficiently and with traceability, to around 1,000 acres/year."
Specifications
- Model: Hi-Spec 4000 TD-S
- Capacity: 4000 gallons (18,000 litres)
- Tyres: 710/50 R26.5
- Technology: Krohne flow meter, NIR sensor, IsoBus
- Injector: Vredo 6m shallow disc