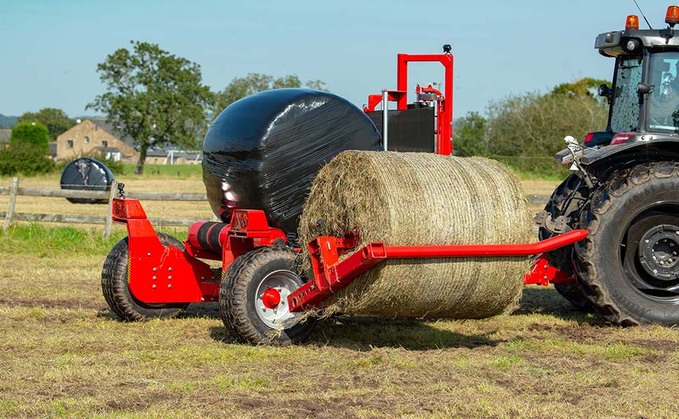
Fitted with several features designed to speed up the wrapping process, we try out Vicon's latest version of its trailed round bale wrapper, the BW2600. James Rickard reports.
Vicon's BW2600 trailed round bale wrapper has been on the market now for about five years and, like many products, it has evolved over time and gained several new features along the way.
The latest iteration of the machine is now available with twin film dispensers and a high speed pack, both of which are designed to speed up the wrapping process.
Built in Ravenna, Italy, the B2600 is Vicon's flagship heavy-duty wrapper offering. This is also complemented by the BW2100, a linkage-mounted static version of the wrapper. You can also specify the BW2600 with remote control capability, should you wish to use it as a static wrapper.
To find out more about the BW2600 wrapper and its capabilities, we teamed it up with the firm's new fixed chamber round baler, the Fixbale 500 (also featured on LAMMA365), to tackle some late cut 2020 haylage.
Wrapper specifications
- Wrapper type: Turntable
- Number of film dispensers: Two
- Maximum bale size: 1,200 by 1,500mm
- Maximum bale weight: 1,200kg (can carry two bales)
- Hydraulic requirement: 35 litres per minute
- List price: £19,928 with high speed pack and twin film dispensers
Chassis
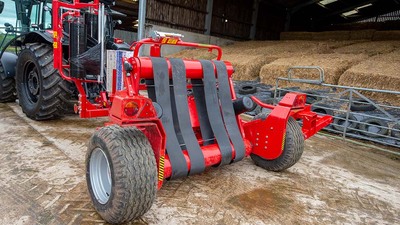
Upon first appearance, the BW2600 looks pretty traditional in its design, with the wrapping table following directly behind the tractor and bales loading onto this via a lift arm on the right hand side.
However, the layout of the machine has been well thought out. In particular, the machine has a wide stance, with the wrapping table sat between the wheels. This means the table can be kept as low as possible on the machine - a very important feature when you are spinning a tonne load. It also means the machine needs no drop mat, as the table is very close to the ground when tipped.
In addition, with the wheels set as far back as they will go, it is also a very stable machine on uneven ground. Balancing out the weight of the lift arm are counter weights on the left hand side of the machine. The chassis itself also features plenty of ‘meat', particularly around the rear-end. As such, the machine looks well planted as it works.
Wrapping table
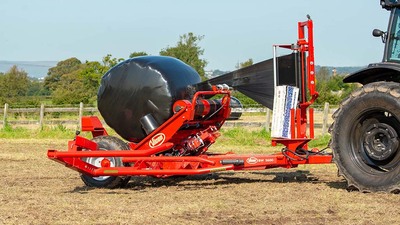
Designed to maximise the wrapper's potential, the firm's high speed kit monitors the table speed, keeping table speed relatively low while the bale settles and levels itself out on the table, before unleashing the full table speed of 32rpm.
The high speed kit is certainly useful for keeping those bales in check which sometimes land on the wrapping table slightly off centre. And it usually only takes a couple of revolutions before the bale is levelled up and the table can get up to full speed. This said, the back plate on the bale lift arm can also be pin-adjusted, to get the bales landing in the right place on the table.
In addition, both rollers on the wrapping table are driven, giving a more positive drive of the bale. Belts, running around both rollers, also help to support and ‘drive' the bale as it is being wrapped.
The table does not require much oil flow to make it spin either (see specifications) - we had to fairly dial down the tractor's hydraulics, to avoid over revving the wrapper.
Dispensers
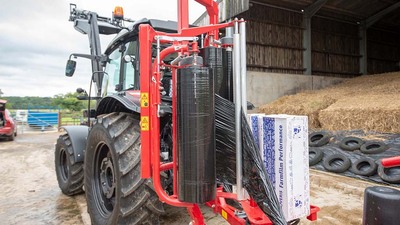
As a twin film dispenser machine, it enables the use of two rolls during the wrapping process. With twice as much wrap going on at one time, compared to single film dispensing, it is a smart way of quickly speeding up the wrapping process, without having to considerably speed up the wrapping table.
However, should the need arise, such as finishing off a roll, you can use the machine with a single film dispenser. This requires the machine to be put in single dispenser mode: firstly by cranking a handle at the rear of the machine, to alter table speed; then you need to ‘tell' the control box it is only using one roll of film, to get the correct number of revolutions. It is a shame that the control box cannot recognise that single mode has been selected when the handle is turned at the rear, though, it is probably rare you will run in single mode.
Integrated into the table is the wrapper's hydraulically-operated cut and hold mechanism. This is powered by its own hydraulic system within the table, with the rotation of the table providing a pumping action for the system.
Control
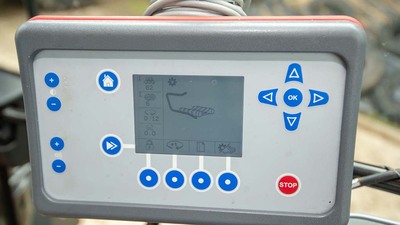
Taking care of wrapper control is the firm's Focus 2 control box and accompanying joystick. For convenience, the independent ‘stick can be positioned where you like it in the cab.
Once the control box is set up, the whole wrapping process, or as much of it as you like, can then be automated. In practice, this sees you manually control the lift arm. Once you have lifted a bale, a quick press of a button on top of the ‘stick starts the wrapping process. This is then paused once the bale is wrapped, leaving you to decide where the bale is tipped. And at any time, the process can be paused and resumed, such as when a roll change is required, for instance.
From the home screen on the terminal you can set the number of layers required, the diameter of the bale and the film stretch, with the wrapper working out how many revolutions of the wrapping table are required. You can also see bale count and table rpm. However, the screen on the box could do with being made bigger and brighter - more like the firm's Focus 3 control box.