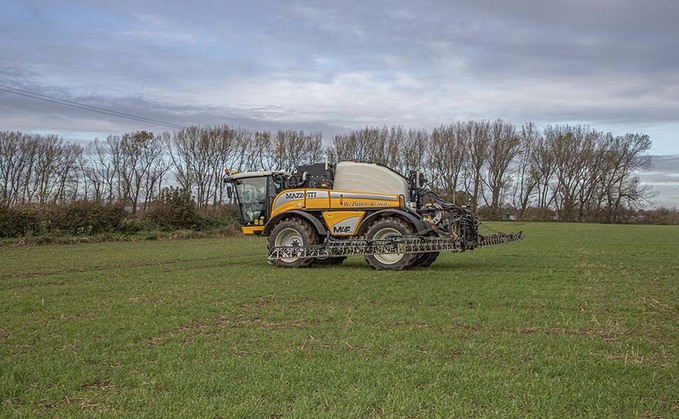
With a keen eye on technology, one Yorkshire grower is making the most of a drone to pin-point areas of crop for spot-treatment, with applications precisely targeted thanks to individual nozzle control. Geoff Ashcroft reports.
When it comes to applying sprays and fertilisers, North Yorkshire grower Graham Potter believes the cost savings alone from only using variable rates are contributing to profitability at the family farm.
"Variable rates are the key to profitability on our farm," says Graham Potter based at Topcliffe Grange, near Thirsk. "We cannot afford to make blanket applications, nor can we apply sprays and fertilisers to areas where we won't see a benefit."
He says a turning point came in 2016, when the farm saw gross margins across one field of winter wheat vary from £690/ha to minus £660/ha. "At that point, we realised that to carry on farming something had to be done to manage variation," he says. "The days of flat rate applications on this farm are finished."
Having recently added a 24m/3,500 litre Mazzotti MAF3580 self-propelled sprayer to his fleet, he believes his precision farming journey is complete. "When I first saw this sprayer at Cereals two years ago, which combined the integration of Greenstar, My John Deere and individual nozzle control, I knew it was what I needed," he says. "We already run John Deere tractors and make the most of auto-steering and telematics, but our previous sprayer - a Bateman RB17 with a 24m, six-section boom - just would not integrate with what we wanted to achieve. And our N sensor would not communicate with the Bateman."
W Potter and Sons grows winter wheat, spring barley, oilseed rape and cover crops on a range of soils extending from blowing sand to heavy clay. It ditched traditional cultivation practices in 2013 and adopted a Claydon strip-till drill. The whole farm has been sampled by Soyl and is frequently resampled to ensure indices are corrected and maintained.
EC soil scanning provides the basis for treatment maps, along with control measures for variable depth subsoiling using a Soyl system installed on a Plowman Brothers five-leg unit to address combine wheelings - but not the removal of tramlines. "Our tramlines are now permanent," he says. "Soil health is critical and I believe that cover crops have a role to play in keeping our soil alive. We do not leave soil bare and we will put a cover crop into stubbles post-harvest."
When it comes to variable rate applications, this too is being refined for zone-specific treatments, thanks to the use of a drone and his latest sprayer's individual nozzle control. "When sat on the sprayer I have a great view of my crops," he says. "If I see areas that need closer inspection, I flag them on the John Deere terminal, then revisit with my drone to carry out a more detailed analysis.
"If necessary, I can create a treatment map to deal only with that affected area," he says. "When you are not treating the whole field, it also takes less time to do the job - and that is another cost saving."
Mr Potter operates a DJI Phantom equipped with a second camera for normalized difference vegetation index (NDVI) imaging, and also a DJI Mavic Air - the latter is sub-250g and is free of the restrictions imposed on his larger aircraft, given the farm's location within a no-fly, Military air traffic zone.
"It takes too long to get clearance to fly the Phantom, so the smaller Mavic lets me analyse immediately with the help of the Skippy Scout app," he says. "It can fly autonomously to the flagged in-field points and provides basic data that lets me create a treatment plan, through Drone Deploy.
"We only use the drone selectively, as a management tool to target immediate issues," says Graham. "And if we cannot bring up the under-performing areas of a field, we will simply take them out of production and sow bird mixes and bee mixes where cereal production just will not pay."
The move to individual nozzle control is creating a reduction of the farm's chemical bill, and Mr Potter adds that there is better compatibility between the sprayer and Gatekeeper farm office software. "I can send variable rate maps to the sprayer, but I cannot yet import ‘as-applied' maps back into the system," he says. "Though we are very close to a fully paperless system, which means better timeliness and faster decision making.
"Variable rate had already reduced our costs, though individual nozzle control means we are now more precise with all our applications," he says. "And we are doing a better job. There are now more beneficial insects around the farm and our soils are showing much better water infiltration."
The Mazzotti has clocked up 300 hours in its first 12 months at Topcliffe Grange and with the latest N sensor fitted, he says application management is bringing yet more cost savings to the business.
Construction of a dedicated sprayer shed complete with chemical store facilities also includes rain water harvesting with a pair of 26,000 litre storage tanks, alongside a 6,000-litre tank filled from a bore hole. "I wanted an insulated, drive-through building that provides enough space to wash the sprayer undercover," he says.
"And because I also use the sprayer for fertiliser applications, my next stage is to install an overhead sprinkler system - on a timer - that can automatically ‘rain' on the sprayer with 1,000 litres of water when it is parked, to remove liquid fertiliser residue.
"We are also going to add a set of stainless steel drip trays on the boom rests, to keep any drips off the machine, when the boom is folded," he adds.
The sprayer shed includes a four-stage bio filter with integrated sediment trap, 1,000-litres of below ground storage and a transfer pump to process washings. The clean water is finally discharged to a bio bed using drip irrigation.
His sprayer was supplied with a few carefully chosen options, including a hydraulic hose reel at the back of the machine, which is used for liquid fertiliser. Water is loaded through the standard fill-point by the induction hopper, though this is an area that needs a little more attention. "There is a useful work light under the cover, but insufficient protection from mud and dirt," he says. "The mudguards need to be longer, to keep the induction area cleaner."
The sprayer came on 340/85 R46 standard row crop wheels and tyres, with Mr Potter investing in a set of Michelin VF600/60 R38s from wheel and tyre supplier Stocks Ag. "Controlling compaction is essential, and the wide tyres run at 12psi, though they can go down to 9psi - then you will struggle to see where the sprayer has been," he adds.
He says the sprayer's Claas-supplied Vista cab is a great place to sit, being both quiet and comfortable. Though controls have prompted a mixed response. "After setting the cruise control speed, I use full joystick movement, which offers precise adjustment up to your chosen cruise speed," he says. "But on the road, the hydrostatic drive does have a delay in it. A recalibration is planned, as this laziness can be scary if you are not expecting it. Fortunately, there is a brake pedal.
"And I cannot action a tank rinse from the cab, though I am told this is likely to be changed."
While daily checks and maintenance are relatively easy, he says that the diesel tank's fill point is high-up, towards the back of the cab and is awkward to access. AdBlue is equally tricky to fill, and is accessed by steps at the back of the nearside front wheel.
"You have to lift the boom off its rest and swing the left-hand side out, to allow the panels to open along with the fold-down steps. Then you can climb up onto the engine platform," he says.
He says the boom does offer a central lock, enabling one side to be folded in-field, to get around obstacles.
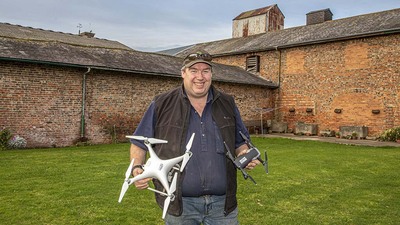
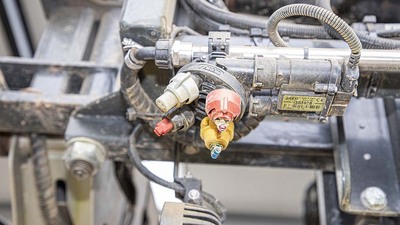
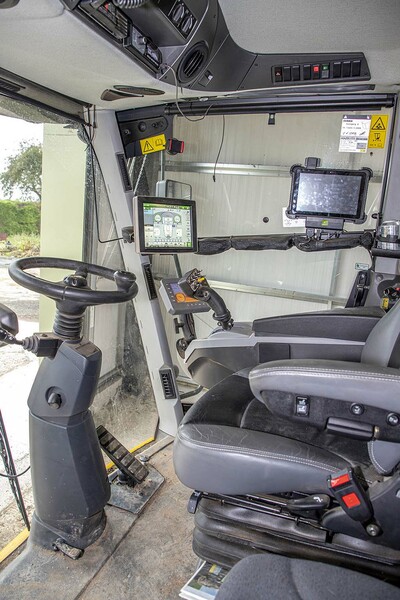
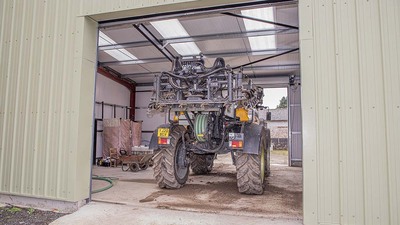
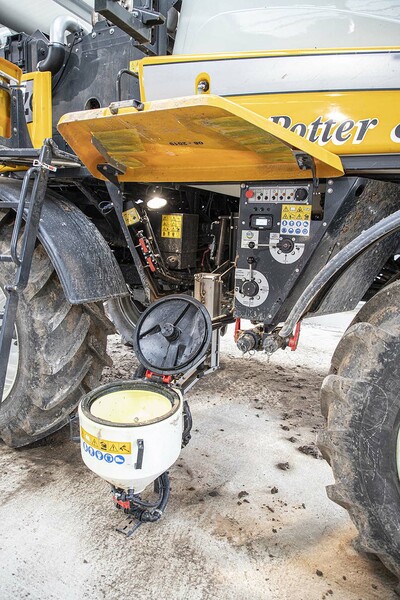
Farm data
- Business: W Potter and Sons, Topcliffe Grange, Thirsk, Yorkshire
- Cropping: 200ha comprising oilseed rape, cover crops, winter wheat, spring barley
- Soil types: From blowing sand to heavy clay
Verdict
While some might question Mr Potter's sanity investing in a new self-propelled sprayer for just 200ha, he would be the first to question if could you afford not to do it.
"Investing in precision farming systems is a long-term plan," he says. "I believe it is the best investment a farm could make, particularly when you consider the savings on offer from reducing overlaps, adopting variable rates and spot-treatments, and also improving soil health.
"The technology we are using, combined with our farm's change in practices, has taught me that I would rather farm 500 acres profitably than make a poor job across 1,500 acres," he says. "Attention to detail is everything."