
With an ageing machine the weak point in the logistical chain, a change of plan was needed for Greens Farming's beetroot campaign, prompting it to purchase a brace of Dezeure reverse tip trailers. Alex Heath finds out how they are performing.
For Greens Farming, the logistics involved in moving 728ha-worth of beetroot from fields around East Anglia, back to its base near Soham, Cambridgeshire, has meant two specialist trailers are now employed.
Greg Colebrook, director of the farming enterprise, explains how transporting the beetroot crop, which makes up a third of its total cropped area, has always been a challenge. And with ageing machinery and closer scrutiny of tractor-trailer operations, a new solution was sought.
Mr Colebrook says; "Transport on the road is a big concern in the area, hence why we choose to use HGVs to ferry the majority of crop from the fields, grown in a 25-mile radius of Soham, back to the base. That means we need a way of getting the beets from the field and into the trucks.
"Previously, we were using a Miedema cleaner loader, but it required a decent sized concrete pad, a man operating it, a loader to receive soil and clean around it, plus it was a slow method, needing three or four trailers to keep the harvesters running while they unloaded. Coupled to that it took significant time to pack up and move it, so when it came to the end of its useful life we looked at our options.
"Another cleaner loader was considered, however, we saw the Dezeure trailers at the LAMMA Show in 2016 and could see the benefit of them in our operation."
As such, in 2017 the farming business purchased a pair of Dezeure TransD20 overloading, reverse tip trailers. Belgian-made, the trailers are novel in their unloading method. Unlike conventional trailers, which pivot at the rear, the Dezeure overload trailers lift at the rear, allowing them to load over the side of an artic trailer.
"The operation is now much quicker and more efficient," says Mr Colebrook. "The trailers have a 20 tonne capacity and came fitted with greedy boards. With most of the beetroot grown on black fen soil that needs protecting and the risk of over loading lorries, we took the greedy boards off. It is of no benefit if one trailer unloads 20 tonnes and the other only 10, then has to wait for the next lorry to come. Removing the boards has left us with 15 tonnes of capacity and enough crop that two trailers unload to fill one lorry.
"The process is quick. They draw on to a track or hardstanding, lift the trailer up, reverse to the lorry and discharge the crop in about eight minutes. They have the ability to discharge in two minutes, but there would be no cleaning advantage to be had.
"We have managed to cut the number of staff needed to transfer the crop from field to road from six to two," says Mr Colebrook. "The price of the two trailers was comparable to a new cleaner loader, but we would still require the same number of trailers and staff in the field, so the long-term cost benefit is greater with the trailers."
Mr Colebrook says the trailers spend most of their time ferrying from the company's Dewulf Kwatro self-propelled harvester, which work well with its 17.5cu.m bunker. They also keep the company's modified Grimme GT300 trailed harvester on the move as well.
Trailers are pulled with a range of tractors. In the first year a John Deere 6155R was used, however, slightly larger machines are now used, including a 6175R from the same manufacturer and JCB 4220 Fastracs. The harvesting campaign is about six months long, starting in June and running through to November. Conditions towards the end of the campaign can deteriorate says Mr Colebrook, however, the relatively small tractors are up to the job, thanks to the trailers' driven axles.
Military grade axles, the same as found on MAN's military trucks, bear the weight and spread it over four 710/50R30.5 tyres with chevron tread pattern. Hydraulically driven from the trailer's on-board pto-powered oil pump, drive is engaged via a clutch system that is controlled from the Secutouch in-cab terminal. The pto pump also provides oil for most of the trailer's functions, including lifting, floor conveyor and cleaner. The rear door is operated from a spool. The trailer also has hydraulic suspension on the drawbar and axles that are self-levelling, as well as a rear steering axle.
A camera at the rear gives the operator a view of the waiting trailer as they back up and the flow of crop over the cleaner.
Fitted at the rear of the trailers is a Grimme-derived TurboCleaner, similar to those found on the German firm's graders. Made up of 13 plastic spiral rollers, these spin, turning and propelling the crop in the trailer underneath. The distance between the rollers is adjustable to take out larger debris. A belt runs below the rollers, catching the soil and depositing it into a box on the trailer's chassis, which can then be hydraulically dumped when the trailer returns to the field. The cleaning system folds vertically when not in use.
Crop is removed from the trailer using chain and slat conveyors. Mr Colebrook says damage to the beetroot is not a major concern. "They are a low dry matter crop, so do not bruise easily, unlike potatoes. I would be concerned using this method of transfer with potatoes, without some sort of fall breaker. However, with various outlets for our beets, including processed and washed, sized and graded fresh product, we do everything we can to keep it in as best of condition as we can. That includes trying to regulate the flow of beets over the cleaner so they are one layer thick to clean them effectively and prevent scuffing."
Mr Colebrook says the trailers have performed well in the three years the company has run them, with few issues to report. Other than electrical problems when they arrived, which he says were promptly dealt with by the factory in Belgium, they have been reliable and described as bombproof. The only other modification the company has made to them is removing the grouping belts at the belt, allowing the full width of the cleaner to fill the trailer as the HGV trailers could become overloaded as a result of filling the corners too much.
"The trailers have definitely increased our infield efficiency and overall logistics, reducing the number of machines in the field and staff needed to get the crop into road going vehicles. In addition they tread lightly on the soil, helping to maintain its integrity, but have the ability to push through the sticky patches thanks to the driven axles," concludes Mr Colebrook.
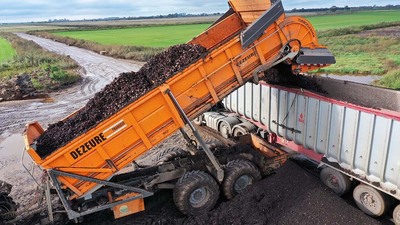
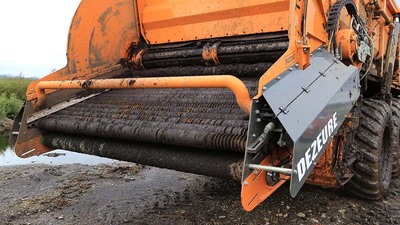
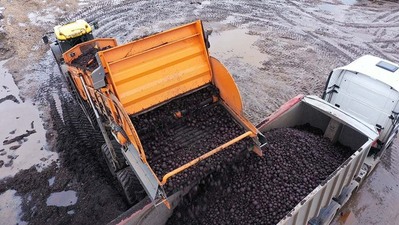
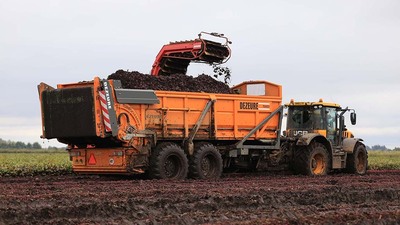
Verdict
An alternative to using a cleaner-loader to transfer beetroot from trailers to road lorries that still removes soil - which is then dumped back in the field - while signficiantly reducing manpower and machine investment.